Vacuum technology powers everything from snack packaging to smartphone manufacturing. Among the tools enabling these processes, oil-sealed rotary vane pumps stand out for their reliability. Let’s uncover how these mechanical marvels turn rotating parts into powerful vacuum creators.
Inside a Rotary Vane Pump: The Key Components
Every rotary vane pump relies on three core parts working in harmony.
A cylindrical stator houses the entire mechanism, with an inlet for drawing gas and an outlet for expelling it. Inside, an off-center rotor spins, creating shifting gaps between itself and the stator wall. Spring-loaded vanes, usually made of carbon composite, slide in and out of the rotor slots. Centrifugal force presses them against the stator, forming airtight chambers that trap and move gas.
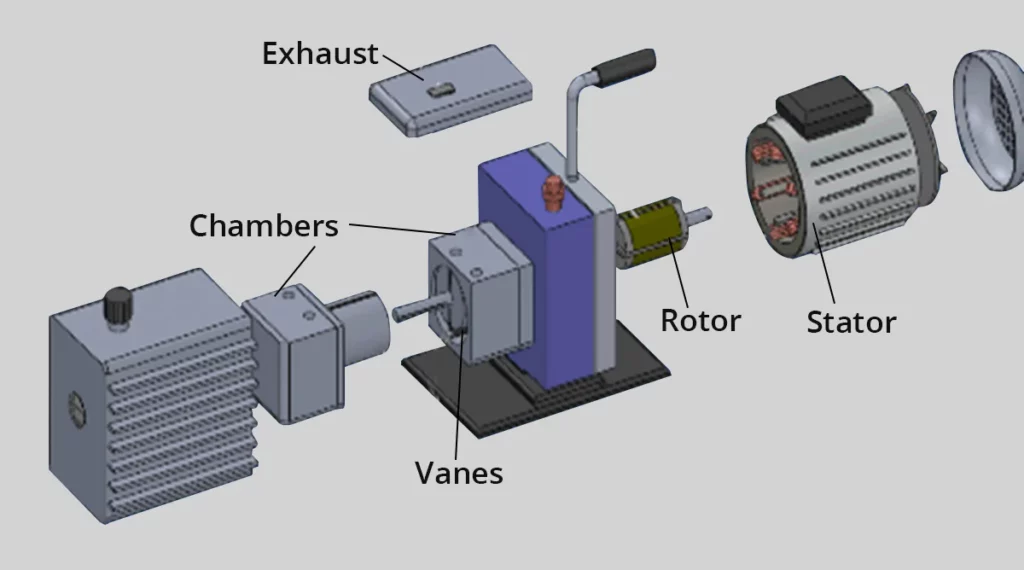
The Four-Step Journey of Gas Removal
Gas molecules follow a precise path from intake to expulsion.
- Intake: As a vane passes the inlet, the expanding space behind it lowers pressure, pulling gas into the pump.
- Isolation: The next vane seals the gas pocket, trapping it between two vanes.
- Compression: The rotor’s off-center motion shrinks the chamber, squeezing gas molecules closer.
- Exhaust: Compressed gas overcomes the exhaust valve’s spring force, escaping into the atmosphere or a secondary pump.
This cycle repeats 1,000+ times per minute, creating a steady vacuum.
Why Oil Matters More Than You Think
Specialized oil isn’t just lubrication—it’s the pump’s lifeline.
- Sealing: Oil fills microscopic gaps between vanes and stator, preventing leaks.
- Cooling: It absorbs heat from compression (up to 80°C in continuous operation) and dissipates it through the pump casing.
- Cleaning: Oil traps fine debris, though these pumps aren’t built for dusty environments.
Using low-quality oil can reduce vacuum efficiency by 40% and accelerate wear.
Single-Stage vs. Two-Stage: Pressure Showdown
Performance hinges on how many compression cycles the gas undergoes.
- Single-stage: Achieves ~1–10 Pa, ideal for HVAC servicing or lab filtration.
- Two-stage: Links two rotors in series, hitting <0.2 Pa for semiconductor manufacturing or electron microscopy.
The second stage acts like a booster, lowering the exhaust pressure the first stage works against.
Handling Water Vapor Without Breaking a Sweat
Pumping humid air risks oil contamination. Gas ballast solves this.
A controlled air leak dilutes vapor during compression, preventing condensation. While this slightly raises the minimum pressure (from 0.1 Pa to ~10 Pa), it’s a trade-off for handling wet environments like freeze dryers.
Where These Pumps Power Progress
From labs to factories, rotary vane pumps drive critical systems:
- Evacuating refrigerators before charging coolant
- Backing high-vacuum pumps in metal coating machines
- Maintaining clean environments in mass spectrometers
Accelerating resin curing in composite material production
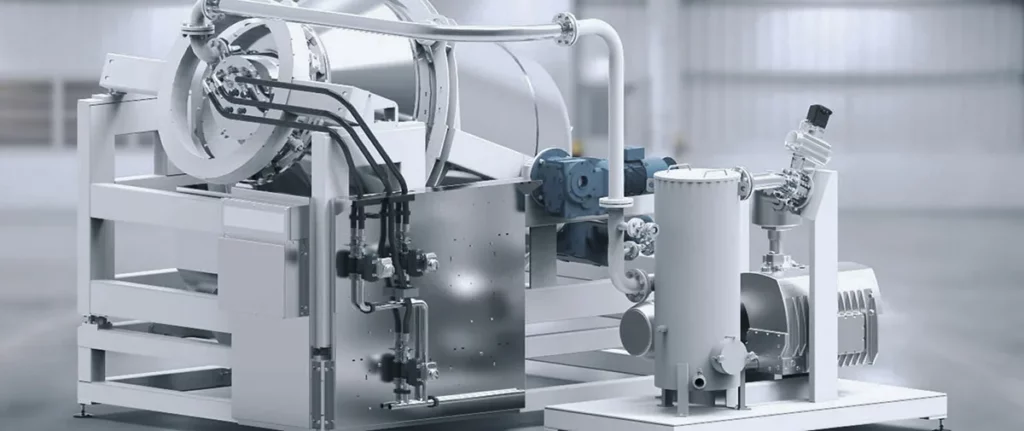
Extending Pump Life: Simple Rules
- Oil Checks: Replace oil every 500–2,000 hours. Cloudy oil signals contamination.
- Filter Care: Clean exhaust filters monthly to prevent backflow.
- Noise Monitoring: Grinding sounds often mean worn vanes or low oil.
A well-maintained pump lasts over 10,000 hours—equivalent to five years of daily lab use.
- Coolink: TOP 3 Global HVAC Vacuum Pump Manufacturer
- Elitevak: Quality Industrial Vacuum Pump Supplier from China