A vacuum chamber effectively removes bubbles from epoxy and silicone by lowering ambient pressure, causing dissolved gases and trapped air to expand, rise to the surface, and burst. Achieving bubble-free results requires proper vacuum levels, sufficient degassing time, and considering the material’s properties and potential chamber compatibility issues.
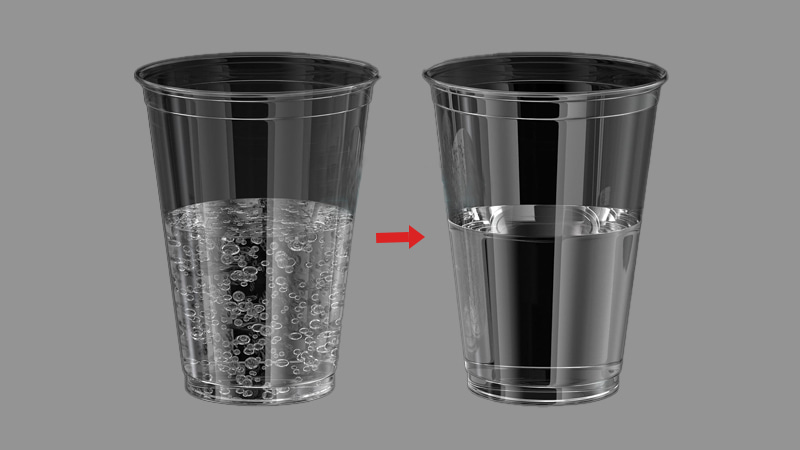
How Does a Vacuum Chamber Effectively Remove Bubbles from Resins?
A vacuum chamber effectively removes bubbles from resins like epoxy and silicone by creating a low-pressure environment. This reduced pressure causes both dissolved gases within the liquid and trapped air bubbles to rapidly expand in volume, reducing their buoyancy and allowing them to quickly float to the surface and burst, expelling the air.
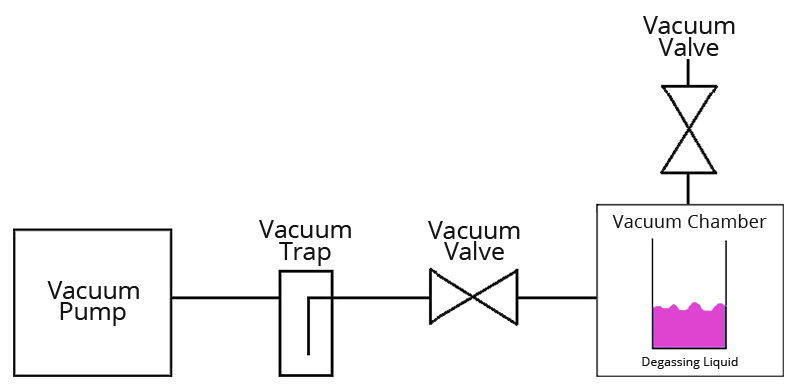
The process of vacuum degassing is quite fascinating and relies on a fundamental principle of physics. When you place a liquid, such as epoxy resin or liquid silicone, inside a vacuum chamber and then use a vacuum pump to lower the pressure, two key things happen. First, the boiling point of any moisture or volatile compounds present in the liquid drops significantly. This causes them to vaporize at room temperature. Second, and most importantly for bubbles, the trapped air bubbles and dissolved gases within the liquid expand rapidly. This is because the external pressure pushing on them is greatly reduced. Think of it like a balloon inflating as you climb a mountain; the lower atmospheric pressure allows it to grow.
Vacuum Degassing Process for Resins:
Step | Action in Chamber | Purpose |
---|---|---|
1. Place Material | Pour mixed resin/silicone into a container within the vacuum chamber. | Prepares material for evacuation, ensures enough headspace for expansion. |
2. Evacuate Chamber | Vacuum pump lowers pressure (e.g., to 50 mbar, then 20 mbar). | Causes bubbles and dissolved gases to expand and rise. |
3. Observe & Wait | Watch bubbles vigorously rise and burst; wait until bubbling stops. | Ensures all air/gas has escaped from the material. |
4. Return to Normal Pressure | Slowly open valve to allow air back into chamber. | Compresses any remaining tiny bubbles, pushes material into detail. |
What Specific Benefits Does Vacuum Degassing Offer for Epoxy Applications?
Vacuum degassing offers specific benefits for epoxy applications by eliminating trapped air and dissolved gases, which significantly improves the final product’s clarity, increases its physical strength and durability, enhances adhesion to other surfaces, and ensures a smooth, flawless finish critical for aesthetic or structural integrity.
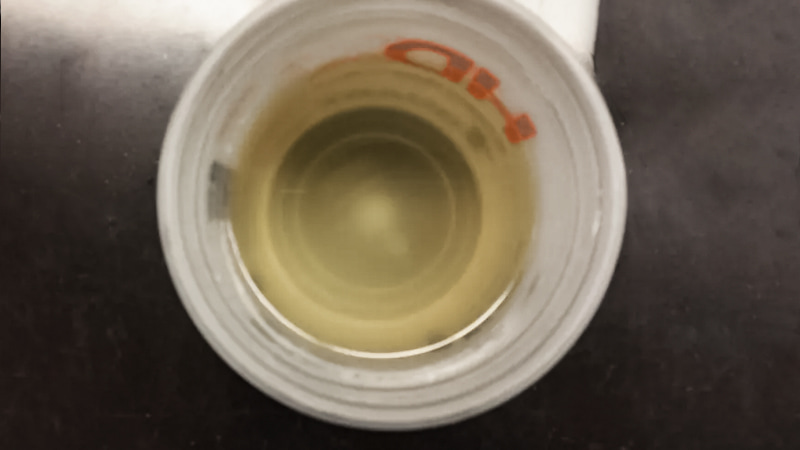
For epoxy resin users, the benefits of vacuum degassing are profound and multifaceted. I have seen how a single trapped air bubble can compromise an otherwise perfect piece. When epoxy cures, any air bubbles remain as voids. These voids become weak points in the material, significantly reducing its physical strength and durability. A bubble-laden epoxy might crack or break more easily under stress, especially in structural or load-bearing applications.
Beyond strength, bubbles drastically affect the clarity and aesthetic appeal of epoxy. For art pieces, jewelry, or clear coatings, bubbles are visually distracting and can ruin the desired transparent finish. Degassing ensures a crystal-clear, professional-grade appearance. Furthermore, bubbles can also negatively impact adhesion. If air bubbles are present at the interface between the epoxy and another surface, they create unbonded areas, weakening the overall bond. This is crucial for applications like wood stabilization for knife handles or pens, where epoxy infuses wood for strength; bubbles would leave weak spots and compromise the stabilization. By eliminating these voids, vacuum degassing ensures a denser, more homogeneous material, leading to superior physical properties and a flawless, high-quality finish that meets demanding standards.
Benefits of Vacuum Degassing for Epoxy:
Benefit | Description | Impact on Epoxy Product |
---|---|---|
Enhanced Clarity | Removes air bubbles that cause cloudiness or imperfections. | Crystal-clear finishes for artistic or optical applications. |
Increased Strength & Durability | Eliminates voids that act as stress points and weak areas. | Stronger, more resilient castings, coatings, and bonds. |
Improved Adhesion | Ensures full contact between epoxy and substrate. | More reliable bonding in layered or composite structures. |
Flawless Finish | Removes surface and internal bubbles for a smooth appearance. | Professional-grade results, higher perceived quality. |
Is a Vacuum Chamber Essential for Achieving Bubble-Free Silicone Results?
Silicone is versatile, but prone to bubbles during mixing and pouring. Is a vacuum chamber a nice-to-have or truly essential for professional, bubble-free silicone projects?
A vacuum chamber is highly essential for achieving truly bubble-free silicone results, especially for mold making, delicate castings, or applications requiring precise detail. While alternatives exist, vacuum degassing is the most reliable method to remove micro-bubbles and dissolved gases that can compromise the strength, appearance, and accuracy of silicone products.
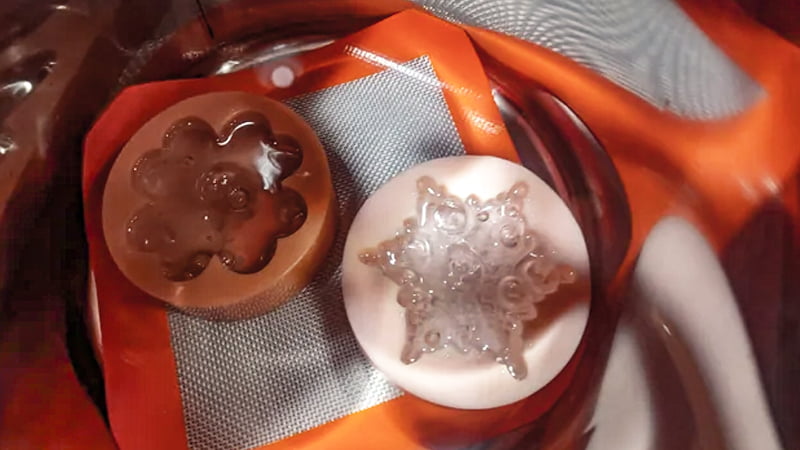
Silicone, even if mixed carefully, traps air. When making molds, these tiny bubbles can form on the surface of the original object, leading to unsightly bumps or imperfections in the cured mold. In casting, bubbles within the silicone itself can compromise the structural integrity of the final piece, especially for thinner sections or functional components. Vacuum degassing ensures that these micro-bubbles expand and escape, resulting in a dense, uniform, and perfectly smooth silicone. This is particularly crucial for applications like prosthetics, medical devices, or high-fidelity reproduction molds where precision and surface quality are paramount. While pressure pots are another option (which compress bubbles to make them invisible rather than removing them), vacuum chambers offer a more thorough removal of trapped gases, leading to a truly bubble-free and durable silicone product.
Why Vacuum Degassing is Essential for Silicone:
Reason for Degassing | Impact of Bubbles on Silicone | Vacuum Chamber Solution |
---|---|---|
Surface Flaws | Pinholes, bumps, and pitting on mold or cast surface. | Removes bubbles clinging to surfaces, ensures smooth finish. |
Reduced Strength | Voids create weak points, leading to tearing or breaking. | Eliminates internal voids, creating a denser, stronger material. |
Loss of Detail | Bubbles can fill intricate details, preventing accurate reproduction. | Bubbles expand and exit, allowing material to fill all cavities. |
Aesthetic Quality | Makes transparent silicone cloudy; visible flaws in colored silicone. | Achieves crystal-clear or uniformly opaque silicone. |
Best Practices: How to Effectively Degas Epoxy and Silicone in a Vacuum Chamber?
To effectively degas epoxy and silicone, ensure your vacuum pump can reach at least 29.5 inches Hg (approx. 25 mbar). Always use a container with ample headspace, pull vacuum until bubbling ceases, and slowly break the vacuum. Crucially, avoid full acrylic chambers for volatile compounds like those in wood stabilization to prevent cracking, opting for tempered glass or stainless steel instead.
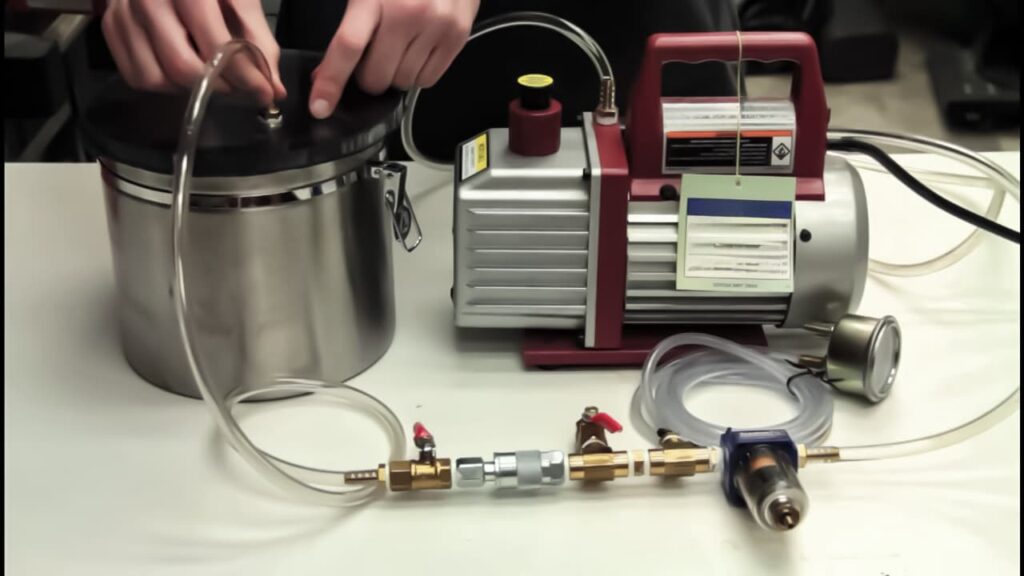
From my experience, the effectiveness of your degassing process hinges on following best practices. First, prepare your materials correctly. Ensure your epoxy or silicone is thoroughly mixed according to manufacturer instructions. Pour the mixed material into a container (e.g., a mixing cup) that is only about 1/3 to 1/2 full. This provides ample headspace for the material to expand and bubble up without overflowing once vacuum is applied. Overflowing can contaminate your chamber and potentially damage your vacuum pump.
Next, focus on the vacuum process itself. Connect your vacuum pump (typically an HVAC vacuum pump is sufficient, able to pull down to at least 20-50 mbar absolute) to the vacuum chamber. Evacuate the chamber, observing the material. It will likely rise significantly and bubble vigorously. Continue pulling vacuum until the material collapses back down and the bubbling largely subsides, indicating that most of the trapped air and dissolved gases have escaped. The process accelerates when the ultimate vacuum achieves 20 mbar.
A critical point I have observed leading to chamber failure, especially with hobbyist setups, is related to the type of chamber material. The vacuum degassing chamber kit is very popular for residential and industrial use. Common chambers include stainless steel chambers with tempered glass lids, stainless steel chambers with acrylic lids, and full acrylic vacuum chambers. During operation, a crack problem for acrylic lids and full acrylic chambers may occur. This is often due to overpressure caused by a wrongly selected vacuum pump model (pulling too strong a vacuum for the chamber’s rating without proper pressure control) or chemical reaction caused by volatile compounds in the resins. A typical wrong application where I have seen acrylic chambers fail is wood stabilization, where certain resin formulations can chemically attack the acrylic over time.
To solve this problem and ensure longevity, I strongly advise against using full acrylic chambers for applications involving volatile compounds, and to replace acrylic lids with tempered glass ones for better chemical resistance and durability. Always ensure your chamber is suitable for the chemicals you are degassing. Finally, slowly break the vacuum by gradually opening a bleed valve. This prevents rapid changes in pressure that could reintroduce bubbles or disturb the degassed material. After the gas, vapors, and moisture are extracted, the pressure is returned to normal, and the degassing process is finished.
Degassing Best Practices Checklist:
Practice | Why It’s Important | Risk if Ignored |
---|---|---|
Proper Container & Headspace | Prevents overflow during bubbling, allows material to expand. | Messy overflows, contamination of pump/chamber. |
Appropriate Vacuum Level | Ensures all air/gas expands sufficiently to escape. | Incomplete degassing, persistent micro-bubbles. |
Patience (Wait for Bubbling to Stop) | Confirms thorough removal of trapped gases. | Bubbles reappear after vacuum release or during cure. |
Slow Vacuum Release | Prevents reintroducing air or disturbing degassed material. | New bubbles form, material surface damage. |
Chamber Material Compatibility | Ensures chamber integrity against chemicals & pressure. | Cracking (especially acrylic), chamber failure, safety risk. |
Final Thoughts
- Coolink: TOP 3 Global HVAC Vacuum Pump Manufacturer
- Elitevak: Quality Industrial Vacuum Pump Supplier from China