Introduction of vacuum forming process, basic types as well as materials used for the forming.
It is very easy to find blister packaging in our daily life. The professional description for blister molding is vacuum forming. The technology is used so widely that you can use small formed parts on your table and large parts in your car.
Vacuum forming technology was born in the 1930s and developed continuously with the times. It is a plastic processing and basically a type of thermoforming. By operating a vacuum pump, a flat plastic sheet is heated and softened, and then attached to the mold surface. After it cools down, the plastic is molded into a desired shape.
The process of vacuum forming
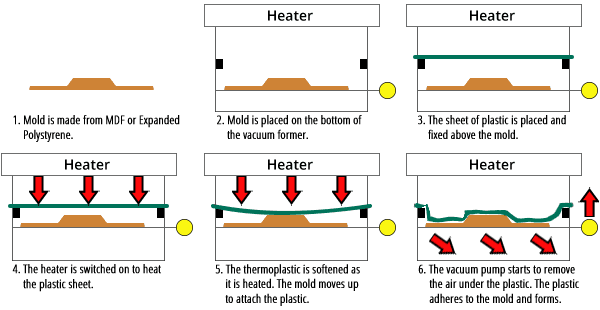
As the most economic method of thermoforming, vacuum forming is easy to use and control. A typical forming process needs only a few minutes. The steps of the process:
- Fix a thermoplastic sheet into place above the mold
- Switch on a heater (electric element) to heat the plastic till it’s softened
- Operate a vacuum pump to remove the air between the mold and the plastic sheet
- The plastic sheet is pliable and attached to the surface of the mold
- Remove the shaped plastic from the mold after it’s cooled down
- Trim the formed plastic to finish the process
Two basic types of vacuum forming
The two main or basic types of vacuum forming are as below:
• Male or Positive Mold Forming
The plastic sheet is clamped above the male mould, and then heated until it is malleable. The soft sheet covers on the convex mold. Remove the air between the sheet and the mold, the plastic attaches to the mold tightly and forms. The convex mold forming features high precision of inner sizes.
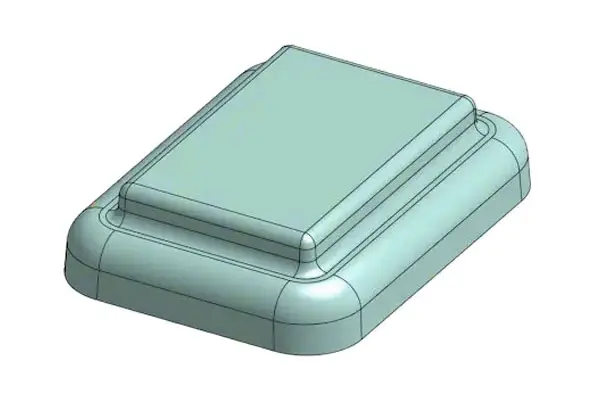
• Female or Negative Mold Forming
Female mold forming is more common. The plastic is fixed and heated till it’s pliable. Remove the air by vacuum pump so that the plastic forms on the concave mold under the atmospheric pressure. Blow out the molded part by compressed air through tiny holes on the mold when the part is cooled. This forming method is used for parts without deep draw. Otherwise the bottom of the part has thin thickness.
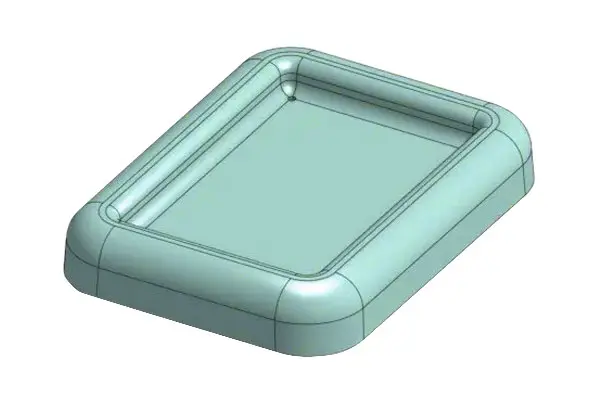
The material used for vacuum forming
Thermoplastics are widely used for vacuum forming. Such plastics have the property of softening on heating and hardening on cooling. HIPS (High Impact Polystyrene Sheet) is the thermoplastic that is most common and easy to use. It can be formed into almost any shape, from wood, structural foam, casting or machined aluminium molds. The HIPS material retains heat and shape when using warm water. It is often used to pack products that are sensitive to taste and odour. The transparent material acrylic is also used for aviation and space applications, such as cabin window covers for military. Vacuum forming is the simplest type of plastic thermoforming which has low vacuum requirement.
Besides HIPS and acrylic, there’re some other materials that are suitable for vacuum blister molding, including:
- PETG (Commonly found in food molds)
- ABS
- Polystyrene (Commonly found in product packaging)
- Polyproperlene (Ideal for resin casting molds)
- Polycarbonate (Commonly found in beverage bottles)
- Polyethylene (Commonly found in sheets and foam sheets)
- Acrylic PMMA (Commonly found in lamp shades)
For this application, the requirement of vacuum is quite low. It’s enough to use a single stage rotary vane vacuum pump to remove the air inside the mold.
Coolink, a TOP 3 Global HVAC Vacuum Pump Manufacturer & Quality Industrial Vacuum Pump Supplier from China