This article introduces the use of cooling and cleaning purges to enhance performance of dry screw vacuum pumps.
For optimal results, it’s advisable to perform purging on dry screw vacuum pumps both before initiating the process and upon its completion. This helps remove any gases and vapors left inside the pump from the compression process. If these leftovers aren’t cleared before restarting the pump, they could overload the motor or damage the screws or pump body.
The cleaning of screw vacuum pumps primarily involve two methods: cooling purge and cleaning purge.
1. Cooling purge
The purpose of cooling purge is to lower the temperature within the pump body and the screw mechanism. During pump operation, the rotation of the screw draws in the gas, which then gets compressed as it moves towards the exhaust end. This compression generates heat, causing the gas temperature to rise rapidly. To prevent potential pump damage, it’s crucial to swiftly dissipate this excess heat.
Ordinarily, atmospheric air serves as the cooling medium. However, when the composition of the gas being pumped makes it unsuitable for air cleaning, an alternative cooling medium like nitrogen comes into play. For standard screw pumps, a designated interface is often situated near the pump’s exhaust end.
The purpose of cooling purge is to lower the temperature within the pump body and the screw mechanism. During pump operation, the rotation of the screw draws in the gas, which then gets compressed as it moves towards the exhaust end. This compression generates heat, causing the gas temperature to rise rapidly. To prevent potential pump damage, it’s crucial to swiftly dissipate this excess heat.
Ordinarily, atmospheric air serves as the cooling medium. If the pumped gas is unsuitable for air cleaning, an alternative like nitrogen serves as a cooling medium. For standard screw pumps, a designated interface is often situated near the pump’s exhaust end.
2. Cleaning purge
Prior to shutting down the pump, it’s crucial to engage in cleaning purge process. Close the main valve on the pump’s intake line and introduce nitrogen or clean air for about 30 minutes. This step is essential to rid the pump’s interior surfaces of any adhesive process materials or gases that might be lingering. This precaution holds particular significance when dealing with corrosive, toxic, or sticky substances like resins.
Steam flushing emerges as an effective method to eliminate lingering traces of compressed gas materials. If there’s a buildup of these remnants, it’s important to ensure that the dry screw vacuum pump doesn’t exert excessive pressure during motor rotation. Especially for active substances such as oligomers, monomers, polymers, and resins, a proper flushing process yields highly favorable outcomes.
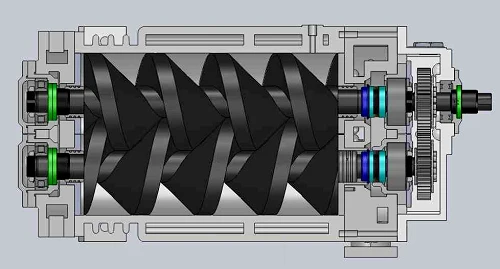
The underlying cleaning purpose revolves around addressing the accumulation of viscous substances within the pump post-operation. Neglecting timely purging and cleaning could lead to heightened motor load, escalated current, and untimely pump wear. Additionally, the accumulation of corrosive gases within the pump might result in the detachment of coatings from critical pump components, thereby impairing overall functionality.
Purging and cleaning materialize through two primary avenues: the use of inert gases like nitrogen or argon, and the application of steam. Timely purging and cleaning are pivotal, both before and after pump operation, ensuring the pump’s optimal function. Whether employing inert gases or steam, maintaining the pressure around 1 kg/cm² strikes the right balance, neither too high nor too low. Excessive pressure risks damaging the oil seals, while insufficient pressure renders the process ineffective.
Operational guide
Connect Inert Gas or Steam: Introduce inert gas or steam at a pressure of 1 kg/cm² through the valve connection. Begin by closing the inlet valve and then opening the inflation valve. Turn the valve on and initiate the pump’s operation, letting it run for approximately 30 minutes. The specific duration depends on the extent of substances accumulated within the screw pump.
Assess Pump Rotation: After halting the pump, manually rotate it by hand. If the rotation feels smooth, it indicates a successful completion of the process. If it’s not smooth, repeat steps 2-3 times.
Continued Operation: Close the inflation valve, restart the pump, and allow it to run for an additional 20 minutes. This step aims to completely expel any remaining liquid from the pump until no liquid is being expelled from the exhaust port. Once done, stop the pump.
Final Checks: Seal the valve and restart the pump. Confirm whether the pump is functioning within normal parameters. Concurrently, ensure that the cooling water system is activated.
Dry Running for Comprehensive Purging: Subsequent to the completion of the cleaning and purification process during the dry screw vacuum pump’s dry run, let the pump operate without load for 20-30 minutes. This crucial step guarantees the thorough elimination of any lingering residues from the pump’s interior, preempting any disruption to its standard operation in the subsequent cycles.
Cleaning agents
Optimal Cleansing Agents: Typically, the most effective agents for cleaning impurities within the pump are 99.99% dry air or nitrogen. These substances offer remarkable results in this context.
Exploring Alternatives: When dry air or nitrogen prove insufficient in thoroughly cleaning the impurities within the dry screw vacuum pump, it’s recommended to consider liquids that possess decomposition capabilities against these impurities. Any non-corrosive liquid with such qualities can be utilized.
Coolink, a TOP 3 Global HVAC Vacuum Pump Manufacturer & Quality Industrial Vacuum Pump Supplier from China