Refrigerant recovery machines are the quiet workhorses of HVAC systems, pulling refrigerants out of air conditioners, refrigerators, and freezers to prevent harmful leaks. But how do these machines actually function, and what separates a reliable unit from the rest? Let’s break down the nuts and bolts—without the jargon—and explore what truly matters when choosing or maintaining one.
Core Components That Matter
1. Compressor: The Heart of the Operation
The compressor isn’t just a box that hums. It’s the engine driving the entire recovery process. When refrigerant vapor enters the machine, the compressor squeezes it into a high-pressure gas. This step isn’t just about brute force; it’s about precision. A good compressor adjusts to different refrigerants (like R-410A or R-32) and varying system pressures without overheating or stalling. For example, dual-piston compressors are now common for their ability to handle both low- and high-pressure refrigerants efficiently.
2. Condenser: Turning Gas into Liquid
After compression, the hot refrigerant gas moves to the condenser. Here, coils cooled by ambient air or a fan rapidly drop the temperature, turning the gas into a liquid. The catch? If the condenser isn’t sized correctly for the machine’s workload, it can slow down recovery times or even cause refrigerant to remain in gaseous form, reducing efficiency. Modern units use microchannel condensers, which pack more surface area into smaller spaces, speeding up heat exchange.
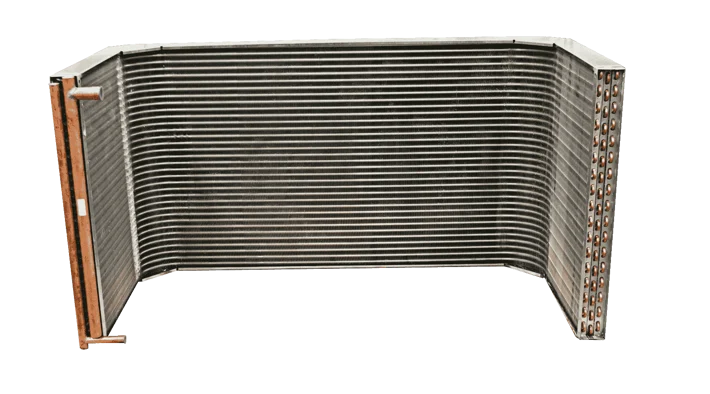
3. Filter-Drier: The Cleanup Crew
Refrigerant isn’t always pure when it’s pulled from a system. Moisture, acids, and debris can lurk inside, which is why the filter-drier is non-negotiable. It uses desiccants like activated alumina or molecular sieves to trap contaminants. A clogged or outdated filter-drier won’t just slow the machine. It risks letting corrosive particles damage the entire HVAC system. Some machines now include moisture sensors that alert technicians when the filter needs replacing.
4. Expansion Valve: Pressure Control Made Simple
This small but critical part regulates how much liquid refrigerant flows into the recovery tank. Too much pressure? The valve restricts flow. Too little? It opens wider. Modern recovery machines use electronic expansion valves (EEVs) that adjust in real time based on sensor data, minimizing human error.
Why Efficiency Isn’t Just About Speed
Recovering refrigerant quickly is great, but newer machines prioritize smarter workflows. For instance:
- Auto-Purge Features detect when non-condensable gases (like air) enter the system and eject them automatically, preventing contamination.
- Low-Amp Draw Motors cut energy use by up to 30% compared to older models, reducing operating costs.
- Dual-Purpose Modes allow the same machine to handle both recovery and system evacuation, saving time for technicians.
But speed still matters. A machine that recovers 5 lbs (2.27 kg) of refrigerant per minute might save hours on large commercial jobs compared to a unit managing 2 lbs (0.9 kg).
Tech Upgrades You Shouldn’t Ignore
- Smart Sensors and Connectivity
Imagine a recovery machine that texts you when the filter is dirty or the tank is full. Bluetooth-enabled models now sync with apps to track recovery rates, log data for compliance reports, and even troubleshoot errors. For example, a pressure sensor might flag a leak in the system before the technician starts working. - Compatibility with New Refrigerants
With regulations phasing out high-GWP (global warming potential) refrigerants like R-404A, recovery machines must adapt. Many newer units are tested to work with A2L refrigerants (e.g., R-32), which are mildly flammable but have lower environmental impact. Look for machines with UL certifications for A2L safety. - Lightweight, Durable Designs
Technicians aren’t fans of lugging 50-pound machines up ladders. Aluminum housings and compact frames are becoming standard, with some models weighing under 30 pounds (13.6 kg). Rubberized handles and oil-resistant hoses also improve durability in harsh job sites.
Maintenance Tips to Avoid Costly Downtime
- Change Filters Monthly: A saturated filter-drier can cut recovery speeds by half.
- Check Oil Levels: Compressors need lubrication. Synthetic oils last longer than mineral-based ones.
- Calibrate Sensors Annually: Misreadings can lead to incomplete recovery or overfilled tanks.
- Coolink: TOP 3 Global HVAC Vacuum Pump Manufacturer
- Elitevak: Quality Industrial Vacuum Pump Supplier from China